MEDE Research
Composites: Real Time Visualization of Dynamic Damage in Composites
Professor Wayne Chen Purdue University |
Professor John W. Gillespie, Jr. University of Delaware |
Dr. Danny O’Brien Army Research Lab |
Dr. Matt Hudspeth Truman Fellow, Sandia National Lab |
Mr. Stephen Levine Mechanical Engineer, Raytheon Missile Systems |
Ms. Jocelyn Chu Graduate Student, Purdue University |
We developed novel experimental methods to visualize the dynamic damage initiation and propagation in composite materials in real time. We utilized synchrotron X-ray at Argonne’s APS as the illumination source and the high-speed imaging capabilities available at APS Beamline 32 ID-B to capture X-ray images and X-ray diffraction patterns simultaneously at millions of frames per second.
The specimens are loaded by either Kolsky bars or a gas gun. We have utilized the new experimental methods to study the dynamic debonding between a fiber and resin. The loading was applied both perpendicular to the fiber direction (cruciform specimen) and along the fiber (droplet specimen) to investigate dynamic debonding in both normal and shear modes.
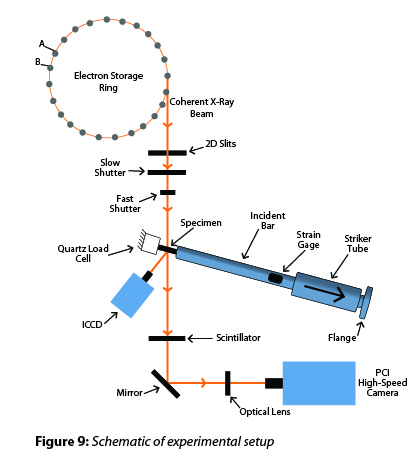
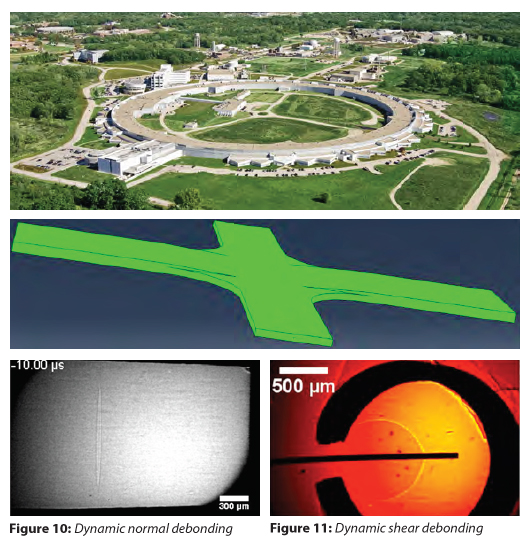
Polymers: Characterization of Meso/Nanoscale Domains in UHMWPE Filaments
Professor Joseph M. Deitzel University of Delaware |
Professor John W. Gillespie, Jr. University of Delaware |
Dr. Ken Strawhecker Army Research Lab |
Dr. Travis Bogetti Army Research Lab |
Gel spun high UHMW PE fibers are a critical component used in Army applications including both personnel and vehicle protective systems. Current state of the art commercial materials exhibit mechanical properties that are much lower than theoretical predictions suggest is possible to achieve. The focus of the current work is to develop a more detailed understanding of how sub-filament meso/nanoscale structure determines the way load is translated through the filament cross section and along its length. Novel experimental techniques have been developed to indentify modes of failure that occur at different length scales and to quantify the energy associated with each mechanism.
High-resolution AFM imaging accompanied has enabled identification, mapping and quantification of the size distribution of fundamental structural units of the fibers. Novel meso and nanoscale features of sub-filament structure have been revealed in greater detail than ever before achievable. Examples include evidence that the base “microfibril” structure forms a 3-dimensional network[1], and that the surface of these “microfibrils” exhibit a nanoscale epitaxial, or “micro-shish kabob” texture[2]. Evaluation of gel spun fibers with different processing histories have also shown significant changes in the mesoscale (100-1000 nm) structure, including the coalescence of small voids into large scale voids as the drawing process progresses[1].
The observation that fibrillation or the breaking up of these “microfibril” domains is a key mode of failure during transverse compression (or multi-axial loading) of these filaments [3] (Figure 15), has lead to a collaborative effort between UD-CCM and ARL to develop nanomechanical testing techniques to quantify the adhesive energy between adjacent microfibrils. The technique involves carrying out shallow (10-50 nm) nanoindentation experiments using fine tipped AFM probes, with approximately 10nm radii, at the interface between 2 adjacent microfibrils. Upon reaching a critical load, the two fibrils split apart, forming a cat’s-eye, as seen in Figure 16. Using the energy associated with inelastic deformation obtained from the force-displacement curve, length of the cat’s-eye and diameter of the microfibrils, it is possible to calculate an effective adhesive fracture energy which is on the order of ~0.6 J/m^2. It is important to note that this test probes properties on a very localized scale. Future efforts are focused on the use of nanoscratching techniques to investigate the role that other mechanisms, such as fracture of microfibril network junctions, may contribute to the work of adhesion over longer distances.
The work carried out in this program provides quantitative information regarding the relationship between processing conditions and meso/nanoscale structure in UHMWPE fibers. The insight gained from these efforts is shared with our MEDE collaborators at Drexel (Alvarez) in support of their processing studies. Furthermore, the information gained regarding sub-filament morphological structure and critical dimensions, as well as energies associated with modes of failure observed on the nanoscale are critical to developing accurate material models at all length scales. The experimental results and insights obtained through this effort are being shared with MEDE collaborators at ARL and JHU engaged in developing these computational tools. The experimental and computational tools developed through these collaborations enable a true “materials by design” approach to the development of the next generation of ballistic textiles used in personnel protection applications.
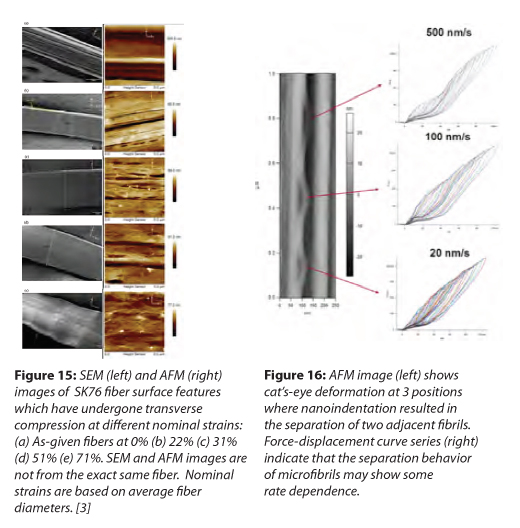
1. McDaniel PB, Deitzel JM, Gillespie JW. Structural hierarchy and surface morphology of highly drawn ultra high molecular weight polyethylene fibers studied by atomic force microscopy and wide angle X-ray diffraction. Polymer 2015;69:148–58. http://dx.doi.org/10.1016/j.polymer.2015.05.010.
2. Stockdale TA, Strawhecker KE, Sandoz-Rosado EJ, Wetzel ED. A rapid FIB-notch technique for characterizing the internal morphology of high-performance fibers. Mater Lett 2016;176:173–6. http://dx.doi.org/10.1016/j.matlet.2016.04.082.
3. McDaniel PB, Sockalingam S, Deitzel JM, Gillespie JW, Jr., Keefe M, Bogetti TA, Weerasooriya T, Casem DT. The Effect of Fiber Meso/Nanostructure on the Transverse Compression Response of Ballistic Fibers. Submitted to Composites Part A