MAT162 Example 2:
Sphere Impact on a Perfectly Clamped Composite Plate
Comparing Composite Damage Modeling between MAT-162 and MAT-054
Benefits of MAT162 progressive damage can be elucidated with simple examples. Consider the transverse impact of a 20mm sphere with an impact velocity of 50 m/s on an 80mm x 80mm x 2mm composite plate modeled with perfectly clamped boundary condition. Shell elements with MAT054 and solid elements with MAT162 damage predictions shows that MAT054 can only model in-plane tension and compression damage, while MAT162 can predict tension-shear along direction 1 & 2, in-plane shear, transverse shear and associated delamination.
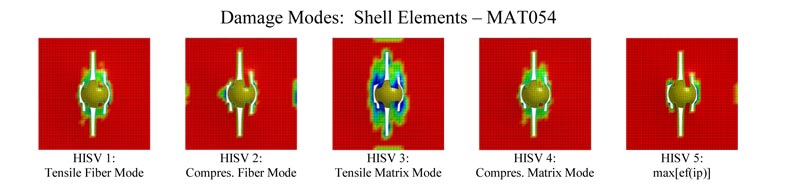
In modeling out-of-plane deformation of any kind, the primary damage mode is tension-shear where MAT162 defines a quadratic damage function with in-plane tension and out-of-plane shear properties for the initiation of tension-shear damage.

The MAT054 equivalent damage function uses in-plane tension and in-plane shear properties instead, and in general fails to account for transverse shear deformation.

The inability of MAT54 in modeling transverse damage modes greatly affects the impact-contact force and associated work done, predicts premature perforation while MAT162 predicts partial perforation and complete rebound of the sphere in case of initial impact velocity of 50 m/s.

A local MAT162 solid model in the anticipated damage region combined with global shell elements can be used to efficiently and accurately model large-scale impact application such as, crash analysis of automotive composite components and aerospace structures under impact conditions.
EXAMPLE 2: Sphere-Impact-on-Composites-SHELL-MAT54.zip This zip folder contains the following KEWORD files. Run the first file. 001-Sphere-Impact-on-Composite-Shell.key 002-control-cards.key 003-Shell-Plate-80mm-x-80-mm-FEM.key 004-700-Sphere-FEM.key 005-parts-partsets-sections-materials-FEM.key 006-100-Node-SET.key 006-nodeset-elementset-segmentset-FEM.key 007-contact-single-surface.key 008-boundary-conditions.key 009-initial-conditions.key 010-loading-conditions.key 011-output-database.key |
In the above file lists, the file 001- is the input file, which includes all other files.